Advantages of the Continuous Cast
Saving Money in the Casting Industry
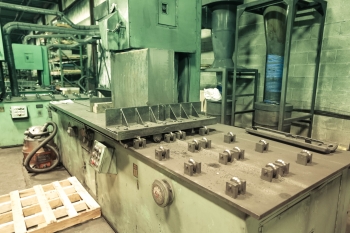
Understand how the continuous casting process produces the highest quality parts for the lowest production costs.
Introduced in the 1950s, the continuous casting process was introduced to manufacturers as a money-saving alternative to ingot casting. Turn the clocks ahead to 2016, and continuous casting is still one of the world's most popular, cost-effective casting techniques. We proudly contribute to the modern continuous casting movement by providing our top-of-the-line Versa-Bar, the industry's premier continuous cast gray and ductile iron.
Our Versa-bar products are perfect for straight-wear applications in the hydraulics industry and, because of their superior metallurgical status, are ideal metals for bushings and bearings.
Before doing business with us, you must understand why we offer the best metal CNC machining & specialty castings services in Wisconsin and the US beyond. To gain this knowledge, you need to consider what continuous casting is and how our role in this process can help you save money.
Contact us for a free quote on continuous cast iron stock.
What is Continuous Casting?
To streamline the production of metal slabs and bars, the continuous casting process made casting metals like brass, steel, aluminum, and copper much more efficient. With the nickname “strand casting,” continuous casting is a simple four-step process capable of improving productivity at any casting company. The steps are as follows:
- First, a steel ladle containing molten metal is titled to pour the metal through a gas-tight refractory tube into a container called a tundish.
- Next, holes at the bottom of the tundish allow molten metals to flow into a series of copper molds at a controlled rate (Copper has great thermal conductivity, so it can cool the metals without sticking to them).
- Then, as the outer shell of the metals solidifies, they are drawn through water sprays and curved pipes to help them cool.
- Finally, the metals emerge as solid strands of brass, copper, steel, Versa-Bar cast iron, or aluminum, cut into manageable strands for further manipulation, storage, or shipment.
Although the process is repetitive and tedious, it is far superior to the ancient method of casting ingots and can save you time and money. Utilizing the continuous casting method is your key to profitability. The diagram below showcases this remarkable process.
Comparing Continuous Casting to Other Common Casting Methods
From blooms to rounds, billets to thin slabs, and conventional beam blanks to hear-net-shape beam blanks, there are several shapes you can create with the continuous casting process. In the past, parts were created by the hands of workers responsible for every step, but today, automated electrical systems have helped improve the precision of continuous casting.
When choosing which casting option you think is best for the parts you need completing, there are three main components you should consider:
- Time Available
- Part Complexity
- Budget
Continuous Casting vs:
Continuous Casting vs Ingot Casting
Before continuous casting exploded in popularity, manufacturers relied on ingot casting to produce slabs and bars. Unfortunately, 5 percent of ingots made in most productions are scrapped because of cracks and butt deformations occurring because of induced stress.
Five percent of 10 blocks made may not sound like the worst statistic in the world, but 5% of 250? That's 13 wasted blocks, which, if made of steel, can cost up to 200 plus dollars in wasted materials! The numbers start adding up if you produce more than 500 blocks a month with ingot casting.
You can optimize your production's cost-effectiveness with no wasted materials during continuous casting. This is the biggest advantage of the continuous casting process. The bars and slabs created are always solid with no cracks, meaning, unlike ingot casting, you will never have to throw away any cracked products. One of the best ways to save money is to increase efficiency. With continuous casting, you can manufacture large amounts of metal slabs and bars in shorter periods than you would with individually pouring your products with ingot casting.
As one of the best continuous cast iron suppliers with our Versa-Bar products, Lawton Standard is your go-to for cost-effective gray and ductile iron continuous cast iron stock and custom metal components.
Continuous Casting vs. Sand Casting
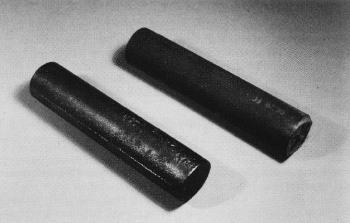
The continuous casting method offers a superior surface finish and eliminates internal porosity and centerline shrinkage.
The majority of metal castings are produced through the sand casting process. However, this more popular choice has deficiencies due to continuous casting. When deciding which way to cast your parts, remember the downfalls of sand casting.
Sand casting can produce several setbacks due to:
- Shifting molds
- A non-uniform cooling rate
- Insufficient materials
- Cracks forming in the sand mold
- Low permeability
- Too high of a melting temperature
Think it ends there? Continuous casting can even cost less. When you want molds created for parts with cores, the process takes much longer, and everyone knows money is time. Need large parts created with the sand casting process? The bigger the mold, the bigger the price.
Continuous casting is superior to sand casting because of its speed and convenience. If you need bars made for your next project, don’t have them poured one by one in molds perfectly created for every part you need. By sawing metal bars into the perfect sizes you need without wasting time on molds, you’ll save money on time and materials when choosing continuous casting over sand casting.
Continuous Casting vs. Extrusion Molding
Known for its ability to force metals and plastics into a desired shape, extrusion molding is a popular option companies worldwide have used when producing simple parts. Unlike continuous casting, the aluminum, iron, and steel extrusion process rams one metal against another with excessive force to force it into a mold.
Extrusion is great for manufacturers who need basic bars and rods, but extrusion will only get you so far if you are seeking more complex parts. Continuous casting has been a competitor with extrusion for years because it offers a similar process at a cheaper price with a greater ratio of success. Need more information on what sets these two options apart? Learn more below about why our customers choose continuous casting over extrusion again and again:
Continuous Casting:
- Less expensive due to lighter weight
- Easy to cast voids and cores without excessive machining
- A faster an cheaper process than extrusion
- High tolerances with complex cast parts
Extrusion Molding:
- Can only create a uniform, cross-sectional shapes
- Surface oxidation is a risk - and can only be corrected with mechanical or acid strategies
- Cannot match the complex casting abilities of continuous casting
- Extruded parts can easily crack inside and out
The Best Supplier of Continuous Cast Iron with Versa Bar and CNC Machining Services
Profitability and productivity are two of the most important benefits any product can supply to a manufacturing company. If you want to invest in your production of slabs and bars, look no further than Lawton Standard’s best brass, aluminum, steel, and copper alternative: Versa-Bar. It’s a superior product, known for:
- Saving manufacturers money
- Increasing machining performance
- The longest-lasting custom metal components
Versa-Bar continuous cast iron offers an affordable and superior alternative to other metals. Its greater metallurgical properties make it superior to older, traditional sand castings. Versa-Bar also contains microscopic flakes of graphite, which help retain oil and keep machine parts lubricated during continuous casting. In addition to reducing production time with our Versa-Bar, Lawton Standard specializes in precision machining services that meet your company’s needs.
Whether pre-machined or finished, we provide value-adding processing services that save you money by increasing efficiency. Lawton Standard offers various machining capabilities, including fluid power, machine tools, construction, and off-highway equipment services.
We provide raw materials and fully machined metal parts, allowing you to customize your supply program completely. Versa-Bar increases the efficiency of your continuous casting process, and our CNC services save you money on transportation, inventory, and manufacturing costs. Thus, we truly are the best metal CNC machining and specialty castings provider in Wisconsin.