Explaining Simple Hydraulic Systems Design
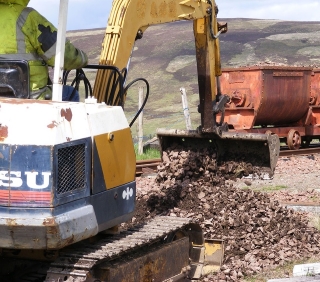
Hydraulic power systems allow heavy machinery to perform massive amounts of work.
Hydraulic system designs are found everywhere, from construction sites to auto shops. Yet despite relying on them every day, most people take these systems for granted.
A hydraulic system’s ability to transform a small space into a source of massive force and work makes it an important factor in manufacturing equipment and heavy machinery.
Principles of Hydraulic System Design
Pascal's principle is the primary principle of hydraulic system design.
In a controlled system, force is multiplied according to the area of the larger weight. Imagine a lever with a small weight on the long side and a larger weight on the smaller side. By applying very little force, a fraction of the larger weight’s mass, to the smaller weight, you can move the larger one.
In a hydraulic system, the weights are replaced by pistons, and the lever is a cylinder full of fluid that cannot expand. A small amount of force is multiplied by the area of the larger piston to produce a greater force. The cylinder is perhaps the most critical aspect of a hydraulic system, responsible for ensuring constant pressure and system protection. A damaged or poorly made cylinder is often the cause of a failed hydraulic system.
Principles of Failure in Hydraulic Systems
The leading cause of hydraulic system failure is cavitation from microjet air bubbles. Caused by simple condensation, water slowly enters hydraulic systems over time. Hydraulic systems, which are usually heated and under immense pressure, will evaporate these small drops of water. Now, under pressure, this small pocket of air will be compressed again and again (sometimes exceeding one million psi) until it bursts, causing cavitation in the interior surface of the cylinder. This erosion creates metal shavings that leave scratches in the cylinder, damage the seal, and exponentially degrade the cylinder over time.
Firms manufacturing these systems demand high-quality cast iron to combat wear and protect system performance.
Fundamental Differences between Hydraulic and Pneumatic Systems
Hydraulic and pneumatic systems are fluid power systems using different means to generate power. Hydraulics uses liquids like oils, and pneumatics uses compressed air or gases.
Pneumatic systems are typically used for lower-power tools with thinner or lighter materials. Hydraulics are used for more powerful machinery, such as those found in the waste management, agriculture, mining, or construction industries.
The most common differences between hydraulic and pneumatic systems are:
- Hydraulics utilizes liquid rather than gas
- There is no delay in movement in hydraulic systems (liquids cannot be compressed)
- Hydraulics can generate greater power than pneumatics
- Pneumatic systems lose more energy due to compressing gas rather than liquid
Examples of Hydraulic Systems
- Tractors
- Scissor lifts
- Hydraulic brake systems
- Sprinklers
- Aircraft
- Pump and motor systems
- ...and many more
Hydraulic systems are everywhere. Why? As with pneumatic systems and all fluid power applications, performing greater amounts of work in smaller spaces offers tremendous economic advantages and efficiency in production.
Protecting Hydraulic System with Continuous Cast Iron Cylinder Construction
As one of the most naturally lubricated metals available, the continuous cast iron Versa-Bar is favored by hydraulic system manufacturers. Many hydraulic systems fail because heat damages the seal over time. Continuous cast iron retains 10% of the heated water, making it ideal for hydraulic system designers looking to minimize system heat.
Continuous cast iron is ultra-durable and resists cavitation. It is also naturally lubricated and can dissipate heat. Thus, hydraulic system cylinder manufacturers prefer the Versa-Bar from Lawton Standard.
Contact us for a quote on high-quality continuous cast iron Versa-Bar today.